耐磨耐黃變聚氨酯樹(shù)脂固化劑
采用TDI大量過(guò)量的方式來(lái)合成耐磨耐黃變聚氨酯樹(shù)脂固化劑,羥基基本上是被TDI上的—NCO包圍,未反應的羥基和TDI上的—NCO反應的概率大,得到的耐磨耐黃變聚氨酯樹(shù)脂固化劑就接近理想反應,TDI過(guò)量越多,反應接近理想反應的程度越大。
TDI過(guò)量得越多,體系黏度越低,繼續增大TDI的含量,按黏度的趨勢,體系黏度會(huì )繼續降低,但凝膠時(shí)間相差已經(jīng)不是太大了,而且凝膠所需時(shí)間已經(jīng)很長(cháng)了,這么長(cháng)的時(shí)間足夠分離時(shí)不凝膠也不固化??紤]到隨著(zhù)體系中未反應TDI含量的增加,會(huì )導致后處理能耗加重,所以確定TDI與TMP的質(zhì)量配比為5∶1。
反應溫度的影響。溫度是TDI-TMP加成反應重要的影響因素。反應溫度越高,反應速度越快,反應完成所需時(shí)間越短,但是反應溫度越高,副反應越多,產(chǎn)物的黏度越大,各種物料越容易被氧化,產(chǎn)物的顏色越深,而且反應溫度越高,TDI分子的2個(gè)—NCO基團的活性差異越小,這樣得到的產(chǎn)物相對分子質(zhì)量分布越不均勻。
另一方面,該反應是放熱反應,外界所給予的能量越多,越不利于反應的控制,反應體系黏度迅速增加甚至有可能造成凝膠。因此,在合成反應中要避免高溫。
溫度對產(chǎn)物的黏度和顏色影響較大,對產(chǎn)物的固體分含量、密度、—NCO值影響不大。TMP在低于40℃時(shí)易析出,因此反應低限溫度不宜低于40℃。本實(shí)驗突破了先低溫再高溫反應的傳統思路,采用一直在較低溫度下反應,適當增加反應時(shí)間。
對苯二酚二羥乙基醚(芳香族二醇擴鏈劑HQEE)-固體是一種對稱(chēng)的芳香族二醇擴鏈劑。它與MDI有著(zhù)良好的配伍性,能明顯提高、改善制品的抗張強度、硬度和回彈性能。
HQEE/MDI是與MOCA/TDI并列的一個(gè)PU彈性體系列,使用該產(chǎn)品的PU一般用于對產(chǎn)品物理性能有高要求的領(lǐng)域.
HQEE是一種代替MOCA的新型無(wú)毒擴鏈劑。廣泛應用于MDI的PUR體系(CPU、TPU、MPU)中。能顯著(zhù)提高PUR制品的耐溫等級、力學(xué)性能(撕裂強度、剪切性、硬度、回彈性等),提高M(jìn)PU膠料儲存穩定性、防止燒焦。很好地改善和調節了PUR的性能。MDI/HQEE常用于對制品物理性能有高要求的領(lǐng)域。如:油井密封件、叉車(chē)輪胎、液壓汽缸密封件、傳送帶等PU制品,對改善高回彈微孔泡沫制品性能很有幫助。
對苯二酚二羥乙基醚(芳香族二醇擴鏈劑HQEE)-固體是主要用于二苯基甲烷二異氰酸酯(MDI)的一種擴鏈劑。這種擴鏈劑體系生產(chǎn)的彈性體主要作重載應用, 例如鏟車(chē)輪胎、油井和液壓設備密封、粗料槽襯里和滑冰板輪等。然而, 若對HQEE的使用性能不了解, 就不能得到最佳產(chǎn)品。
一般來(lái)說(shuō), 用MOCA為擴鏈劑生產(chǎn)彈性體的設備, 也能用于HQEE體系的生產(chǎn)。但二者的工藝是明顯不同的。HQEE和MOCA在將近相同的溫度(100℃)熔融,但MOCA會(huì )出現過(guò)冷而不結晶。HQEE不會(huì )出現過(guò)冷,但加工設備中必須保持110-116℃(最高122℃)。HQEE熔罐必須均勻加熱到110℃以上,緩慢攪動(dòng)以防止表面和罐壁上起沫。用于HQEE的工藝設備管線(xiàn)要適當地保溫和加熱, 以防止出現“ 冷點(diǎn)” 而造成管線(xiàn)堵塞和HQEE預聚物混合比的誤差。
MOCA/預聚物的混合比可在理論值的90~100%范圍內變化, 仍能得到理想的制品。然而, 對于HQEE體系, 必須精確控制二醇擴鏈劑/預聚物的比例, 才能得到最佳產(chǎn)品性能。預聚物也應保持在110℃下,并且在HQEE與預聚物混合后, 必須維持溫度以防止HQEE結晶。整個(gè)成型溫度必須保持在110-120℃之間。對于薄制件需要較高的溫度。低于上述溫度時(shí)將導致HQEE結晶出現疵點(diǎn)。烘箱或模具加熱設備必須超過(guò)所要求的成型溫度。
未催化的HQEE/MDI彈性體的流化時(shí)間, 對于薄制件(如墊圈)大約需2小時(shí);對于厚制件(如鏟車(chē)輪胎)能明顯減少脫模時(shí)間。
為了降低擴鏈劑的熔融溫度以達到降低加工溫度的目的, 可將HQEE與其它二醇、三醇和工業(yè)擴鏈劑混合使用。常用的比例是HQEE為80-90% , 二醇或三醇為10-20%。
制品的某些缺陷, 可通過(guò)改進(jìn)操作而避免。表面白霜是由于擴鏈劑/預聚物混合或成型溫度太低, 或是由于模具溫度太低而造成。模壓制品的表面刻痕是由于混合不當或模具過(guò)早關(guān)閉而引起的。模制品表面翹曲則表明模具可能關(guān)閉過(guò)晚。
結果表明,反應不僅能夠進(jìn)行,而且趨于理想反應,所得到的反應產(chǎn)物顏色淺,相對分子質(zhì)量小,黏度低,流動(dòng)所需溫度低,這樣的產(chǎn)物適合在薄膜蒸發(fā)器中進(jìn)行游離TDI的分離。因此,該合成反應選擇在較低溫度下進(jìn)行,延長(cháng)反應時(shí)間使反應完全,反應溫度控制在50℃,1h滴加完全后,再繼續反應4h,得到的加成產(chǎn)物直接在薄膜蒸發(fā)器上進(jìn)行游離TDI的分離,得到了性能優(yōu)良的無(wú)毒固化劑。
加料方式對合成預聚物性能的影響。在耐磨耐黃變聚氨酯樹(shù)脂固化劑的合成工藝中,加料方式有多種,而且不同的加料方式對產(chǎn)物影響較大。本文試驗了3種加料方式,第1種是一次加料,即將脫水的TMP、TDI和醋酸丁酯一起加入到反應器中進(jìn)行反應。該法的優(yōu)點(diǎn)是工藝簡(jiǎn)單,節約設備,縮短反應時(shí)間。
然而一次加料的方式中,反應過(guò)程中的溫度難控制,產(chǎn)物相對分子質(zhì)量分布不均勻,黏度大。第2種是將固體的TMP分次加料,即分多次將固體TMP加到TDI-醋酸丁酯溶液中進(jìn)行反應。第3種是將脫水后的TMP保溫在60℃以上(防止TMP析出),在攪拌下將TMP溶液滴加到TDI-醋酸丁酯溶__液中進(jìn)行反應。
在第3種工藝中,TDI相對于TMP過(guò)量,4位—NCO反應幾率較大,因而反應均勻。而且滴加法反應過(guò)程容易控制,反應趨于理想化,合成的產(chǎn)品相對分子質(zhì)量分布均勻,黏度低,在薄膜蒸發(fā)器中分離游離TDI過(guò)程中操作穩定。所以選擇用第3種加料方式進(jìn)行加料。
溶劑的影響。在相同溫度及固含量,不同溶劑體系的黏度是不相同。早期用環(huán)己酮作溶劑以完成均相加成反應,但產(chǎn)物顏色深,氣味大,不宜使用。
后來(lái)的研究中,多用甲苯、二甲苯和醋酸丁酯的混合溶劑,效果較佳。本研究中,采用單一溶劑醋酸丁酯,是因為單一的溶劑其物理特性單一,便于后處理中的分離,分離后的溶劑循環(huán)使用。
合成了相對分子質(zhì)量小、黏度低、流動(dòng)所需溫度低的適合在薄膜蒸發(fā)器中進(jìn)行游離TDI分離的TDI-TMP預聚物。
文章版權:張家港雅瑞化工有限公司
http://m.2cdigitalleads.com
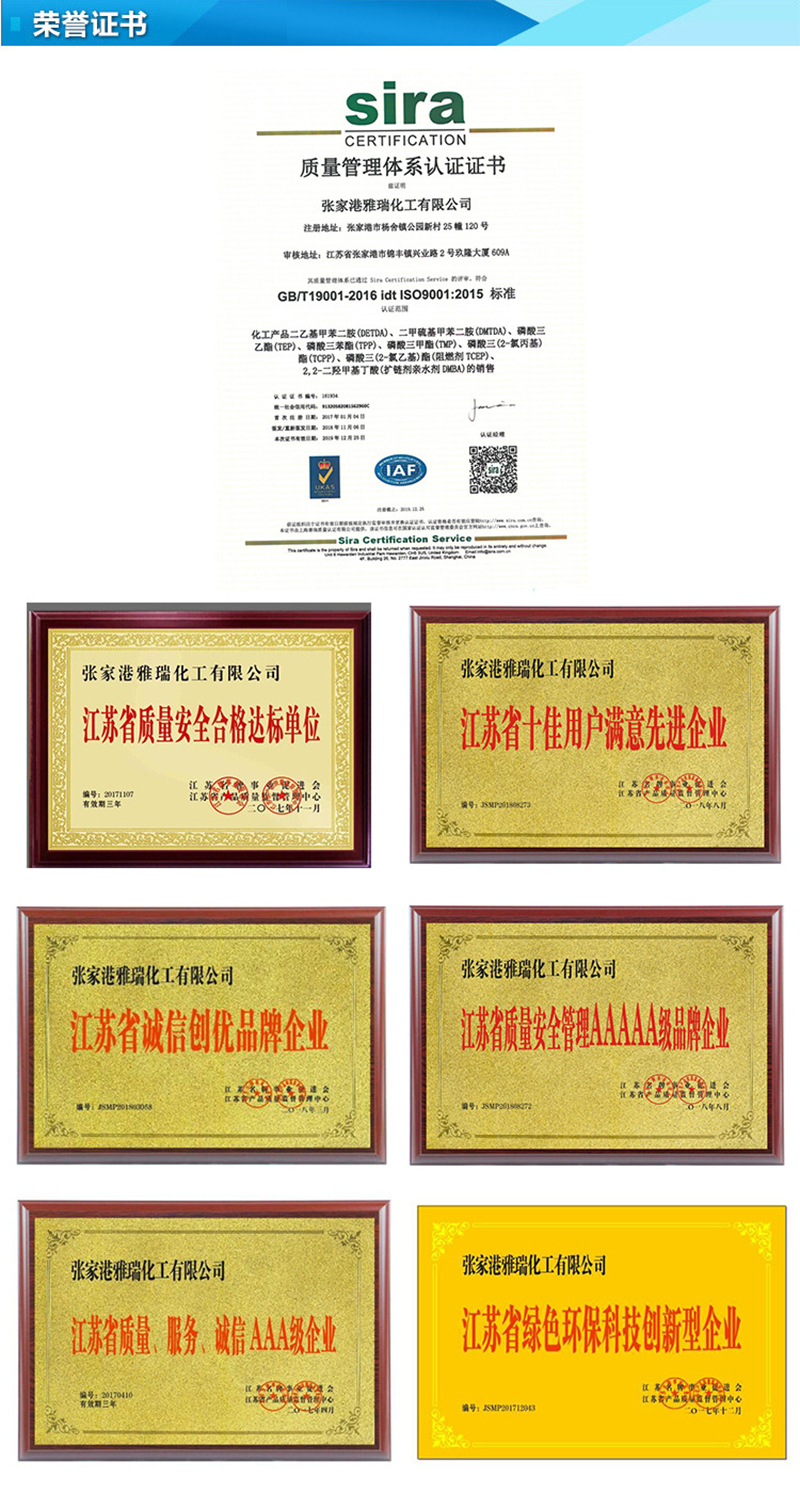