聚氨酯擴鏈劑對性能的影響
聚氨酯擴鏈劑對性能的影響實(shí)驗步驟:分別以MOCA、DMTDA、BDO為擴鏈劑與PPO按摩爾比12∶9配成B組分,與同一批的預 聚物[w(—NCO)=13%]反應制備RIM聚氨酯彈性體。
聚氨酯擴鏈劑對性能的影響實(shí)驗可知,由DMTDA制備的彈性體與MOCA制備的彈性體在力學(xué)性能上基本相同,而在反應速度上DMTDA則表現出了反應活性高的優(yōu)勢,4min內即可脫模;MOCA則由于結構中—NH2基鄰位Cl原子的空間位阻效應和電子誘導效應而導致其活性降低,固化時(shí)間長(cháng),不適合RIM工藝。
聚氨酯擴鏈劑對性能的影響實(shí)驗顯示,與胺類(lèi)擴鏈劑相比,由脂肪族擴鏈劑BDO制備的彈性體則強度較差,這是因為胺類(lèi)擴鏈劑與二異氰酸酯反應生成得脲基的極性比由二醇擴鏈劑得到的氨酯基的極性強,相應的剛性鏈段也易聚集在一起形成硬段,從而氫鍵更多,性能更好。
硬段含量對彈性體性能的影響。半預聚物法制備聚氨酯彈性的過(guò)程中,通過(guò)調節B組分中擴鏈劑、聚醚的配比可制得不同硬段含量的聚氨酯彈性體。以w(—NCO)=13%的L-MDI/PPO預聚體為A組分,分別同DMTDA/PPO質(zhì)量比為1/8、2/8、3/8、4/8、5/8 的B組分反應。
隨著(zhù)硬段含量增加,彈性體的硬度、拉伸強度、撕裂強度均隨著(zhù)硬段含量的增加而增加,扯斷伸長(cháng)率則降低。這歸因于DMTDA中含有苯環(huán)結構及其—NH2與異氰酸酯(—NCO)反應生成具有較高內聚能和極性的脲基結構。
脲基作為硬段和軟段聚醚具有不相容性,導致聚氨酯結構上發(fā)生微相分離。隨著(zhù)硬段含量增加極性基團增多,硬段間形成大量氫鍵,分子間作用力增大,微相分離程度提高。
4,4'-亞甲基雙(2-甲基-6-乙基苯胺),擴鏈劑固化劑MMEA應用:聚氨酯彈性體、聚脲樹(shù)脂固化劑及環(huán)氧樹(shù)脂固化劑.
包裝: 25kg/桶
4,4'-亞甲基雙(2-甲基-6-乙基苯胺),擴鏈劑固化劑MMEA特性:
分子量:282.4231
密度:1.039g/cm3
熔點(diǎn):85 °C
沸點(diǎn):443.1°C at 760 mmHg
同時(shí),硬段微區逐漸形成結晶,并且結晶度隨硬段含量的增加而逐漸提高。硬相不溶于軟相中,而是分布其中,形成一種不連續的微相結構,在軟段中起到物理交聯(lián)點(diǎn)的作用,并起增強作用,使彈性體的性能得到提高。
異氰酸酯指數對彈性體性能的影響。采用同一批L-MDI/PPO[w(—NCO)=13%]為A組分,DMTDA/PPO(質(zhì)量比為3/8)為B組分合成了彈性體,比較了不同異氰酸酯指數(R)對彈性體性能的影響。R即n(—NCO)與 n(—OH)和n(—NH2)(活性氫)和之比。
當R值由0.9增至1.0時(shí),彈性體的硬度增加,扯斷伸長(cháng)率降低,拉伸強度、撕裂強度明顯增加。這是因為在R小于1.0時(shí),反應體系中—OH和—NH2過(guò)量,且—NH2活性高,導致部分聚醚未參加反應,在體系中起到內增塑作用,使制品硬度降低,強度下降。
當R值達到1.05時(shí),—OH和—NH2全部反應,且過(guò)量的 —NCO基團和氨基甲酸酯反應生成脲基甲酸酯基,適當交聯(lián),彈性體性能得到進(jìn)一步提高;而當 R值達到1.1時(shí),形成過(guò)多脲基甲酸酯鍵,交聯(lián)過(guò)度,增大了剛性鏈間的距離,妨礙了剛性鏈的氫鍵結合,使大分子鏈間的聚集作用得到減弱,導致彈性體扯斷伸長(cháng)率大幅度下降。
催化劑用量對彈性體性能的影響。半預聚物法制備聚氨酯彈性體時(shí),由于聚醚中—OH/—NCO的反應活性遠不如擴鏈劑中的—NH2/—NCO,需添加有機錫類(lèi)催化劑DBTDL使軟硬段反應平衡。表5為催化劑用量對彈性體性能的影響。
當催化劑質(zhì)量分數由0.1%增至0.4%時(shí),彈性體的拉伸強度、扯斷伸長(cháng)率及 撕裂強度得到了一定程度的提高,這是因為在聚氨酯反應中—NCO/—NH2反應速度大大快于—NCO/—OH的反應速度,硬段反應過(guò)快會(huì )造成硬段過(guò)早從軟段中分離出來(lái),從而使彈性體表現出脆性。有機錫類(lèi)催化劑DBTDL對—NCO/-OH的反應有強催化作用,而對—NCO/—NH2的反應無(wú)明顯催化作用。
添加DBTDL在一定程度上平衡了軟硬段間的反應速度,有利于硬段均勻地分散在軟段中,起到物理交聯(lián)點(diǎn)的作用,從而提高了彈性體性能。催化劑質(zhì)量分數超過(guò)0.4%后對性能影響不大,這是因為軟段反應速度已達極限。
文章版權:張家港雅瑞化工有限公司
http://m.2cdigitalleads.com
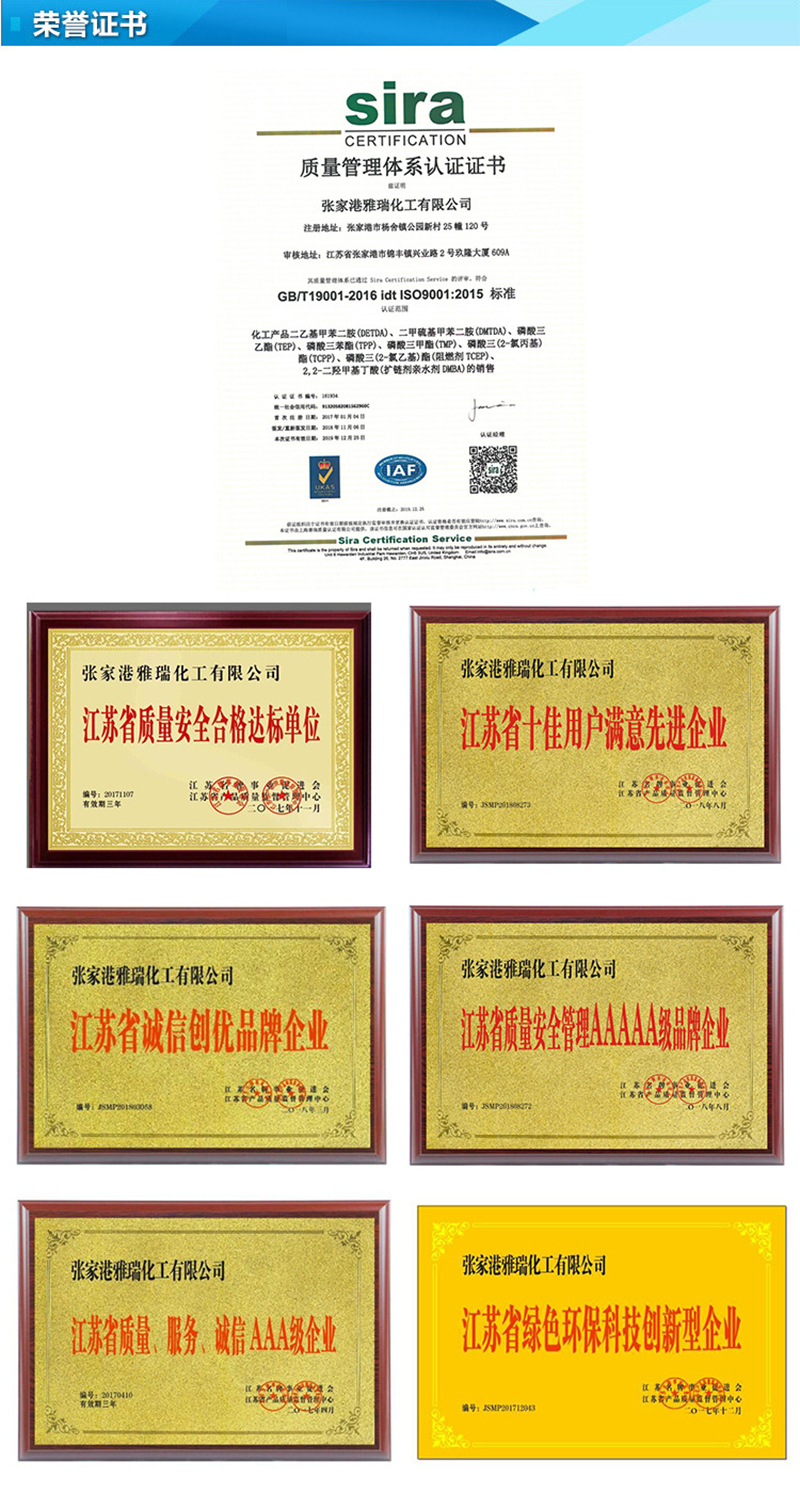